|
|
|
TM 9-2815-225-34&P
3-47. TURBOCHARGER REPAIR (Contd)
LOCATION/ITEM
ACTION
REMARKS
b. Cleaning and Inspection (Contd)
27. Wheel and shaft (20)
Inspect for:
a. Turbocharger seal groove
Use crocus cloth to smooth out
damage.
small grooves and marks.
b. Thrust edge for scratches.
c. Cracks.
Use dye solution. Refer to
MI-I-6866 for inspection and pene-
trant methods. Discard if cracked.
d. Damaged threads.
Discard if damaged.
28. Wheel and shaft (20)
Inspect for:
weld area
a. Chips or scratches near
Discard if chipped or scratched.
weld area.
b. One hole in welded area
Visual inspection.
allowed. Maximum hole
diameter of 0.080 in. (2.032 mm)
is acceptable.
c. Holes in weld area not to
Dye solution crack detection
exceed 0.015 in. (0.381 mm).
method. Very small holes that
cannot be seen in visual inspec-
tion are allowed.
d. Cracks in weld area not to
Use a suitable crack detector
exceed 0.3750 in. (9.525 mm)
other than visual inspection.
in length.
e. Not to exceed three cracks in
weld area.
f. Minimum distance of 0.250 in.
(6.35 mm) between cracks.
g. Cracks on circumference of
welded area not to exceed
0.0625 in. (1.587 mm) in length.
h. Discard if fails to meet any of
the above conditions.
29. Wheel and shaft (20)
Inspect for shaft runout. Not to
Remove aluminum deposit with
circumference
exceed 0.0005 in. (0.0127 mm).
crocus cloth before inspection.
Rotate and support shaft in
Vee-block and position dial indica-
tor to determine runout. Discard if
exceeded (see illustration).
3-284
|
|
|
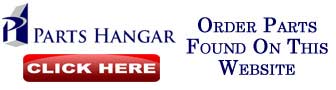 |
Privacy Statement -
Copyright Information. -
Contact Us